Available with: Microsoft 365 Copilot
Manufacturing scenario: Recall management
Scenario
Using Copilot for recall management
Use AI to monitor plant outputs to detect quality issues. When a recall is required, Copilot can assist the team with communications and collaboration to minimize costs and reputational damage.
A chemical plant’s quality engineer identifies elevated levels of benzene, a known carcinogen, within a specific batch of products – used as industrial solvents and has been shipped to customers.
Microsoft 365 Copilot Chat1
Benefit: Support efficient review and understanding of regulatory documents, guidelines on Permissible Exposure Limits (PELs) etc., and the next best actions for recall management
Assess and identify the risk category levels, safety threshold deviations, and assemble the recall committee to warrant the outreach.
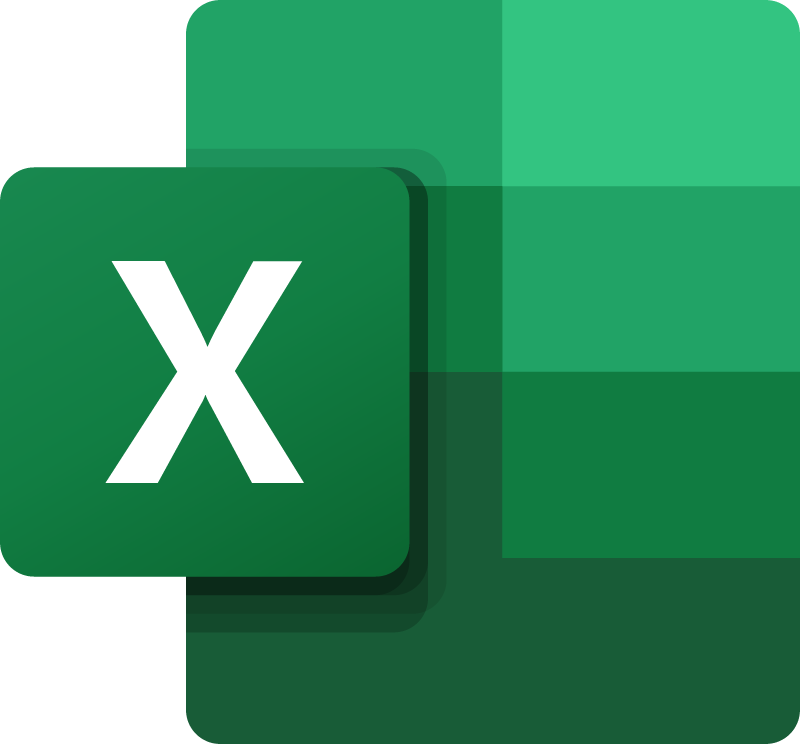
Copilot in Excel
Benefit: Extrapolate the risk category and degree of impact by accessing customer purchase data and distribution records to identify companies and industries that received the contaminated products
Notify relevant authorities / stakeholders (e.g., distributors, downstream manufacturers) across channels with clear instructions on product handling and secure return procedures.
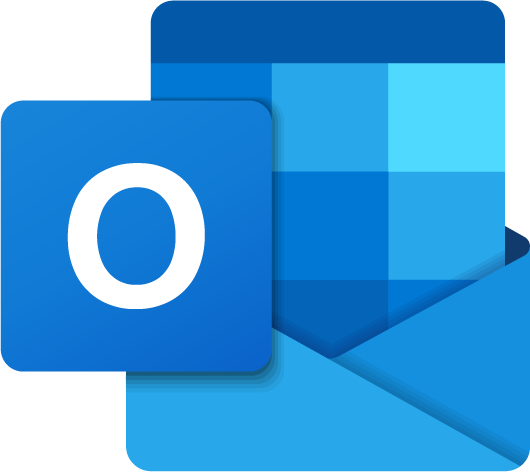
Copilot in Outlook
Benefit: Automate distribution lists, draft customized notifications and ensure timely updates in communication portals for real-time updates, safety information, and contact information for inquiries
Analyze transportation networks, regulatory requirements, and available resources to suggest the safest and most efficient routes for product recovery.
Microsoft 365 Copilot Chat1
Benefit: Collaborate effectively across teams (e.g., legal, transportation) in a secured manner and generate progress reports to plan product recovery execution
Examine the specific factor(s) that caused the contamination – such as equipment malfunction, inadequate purification steps, or human error to facilitate quicker resolution.
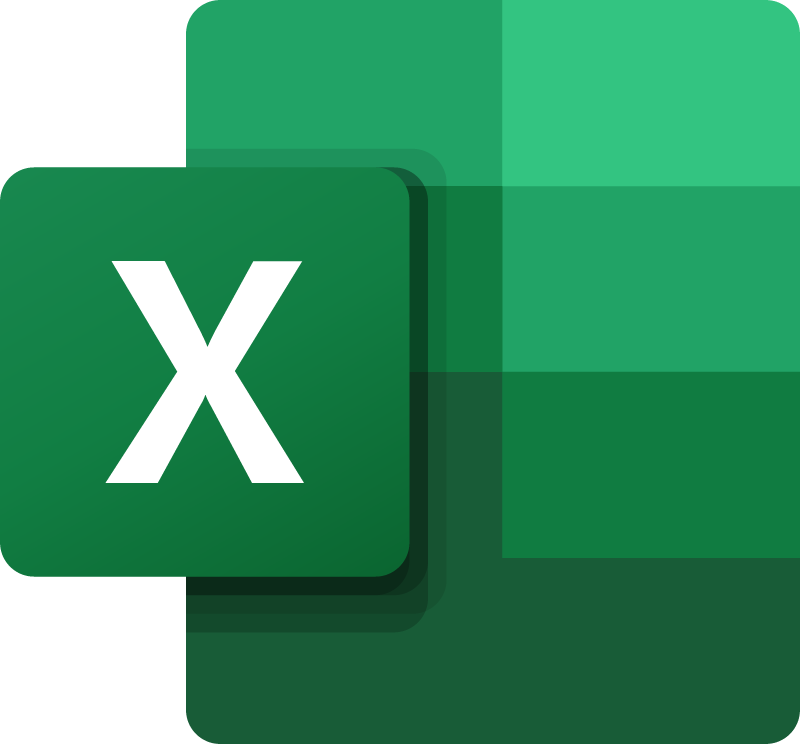
Copilot in Excel
Benefit: Analyze production data, quality control records, and sensor readings from the affected batch, focusing on potential contamination points
Evaluate the overall recall management’s success and update procedures to prevent similar future batch issues.
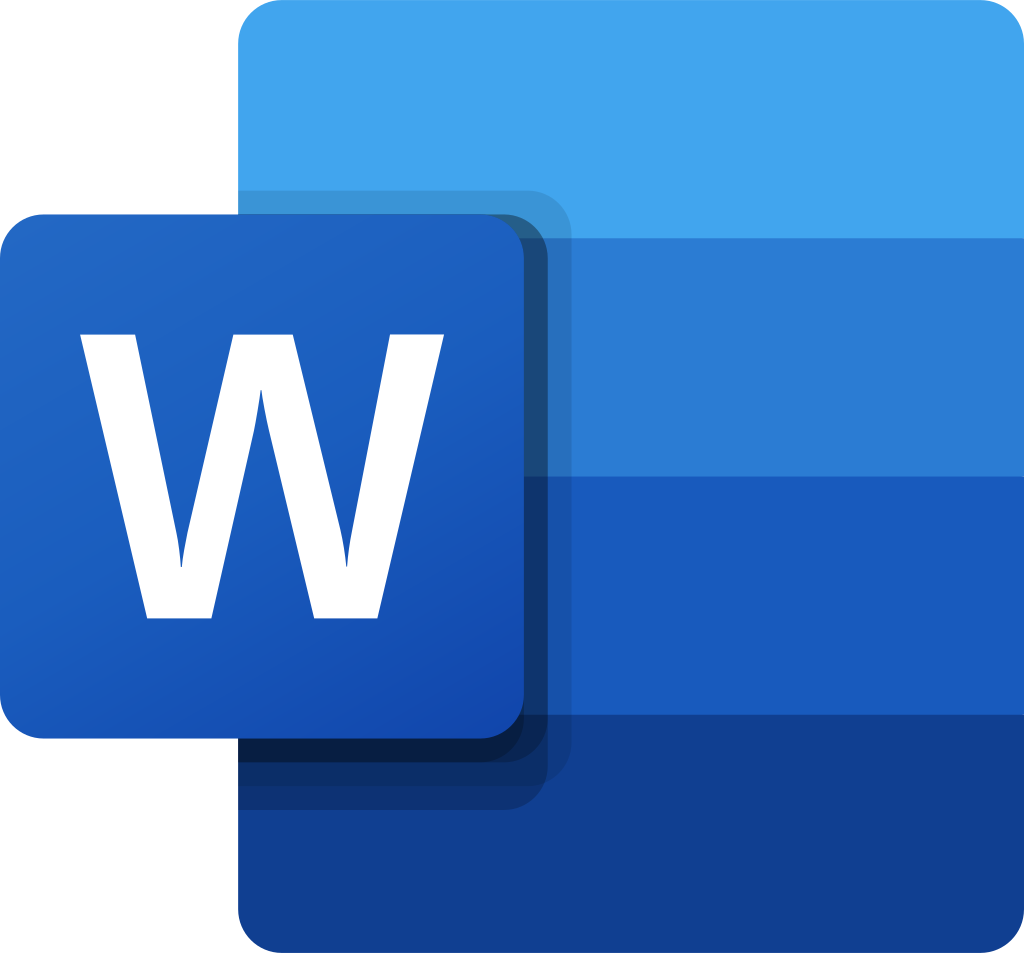
Copilot in Word
Benefit: Document and socialize the recall issue with the latest corrective actions, root cause(s), and improved processes, quality controls, safety measures, and best practices
1Access Microsoft 365 Copilot Chat at m365copilot.com, or the Microsoft 365 Copilot Chat mobile app and set toggle to “Web”.
2Access Microsoft 365 Copilot Chat at m365copilot.com, the Microsoft 365 Copilot Chat mobile app, or the Microsoft 365 Copilot Chat app in Teams, and set toggle to “Work”.
3AI Agents allow Copilot to access your organization-specific apps. In the past this would have required an API call to get data from a system of record.
The content in this example scenario is for demonstration purposes only. You should evaluate how Copilot aligns with your organization’s business processes, regulatory requirements, and responsible AI principles.
What's next
Explore more Manufacturing Scenarios
Manufacturing Scenario LibraryStart using Copilot
Go to the Copilot app to try a new scenario now. Everyone can start with Copilot Chat and if you are licensed Microsoft 365 Copilot connects to your work data and apps.
Start using CopilotView all downloadable content
Download our functional scenario kits, scenario guides, and day in the life guides to accelerate your Copilot implementation.
View downloads